Transform Manufacturing
with Enspct
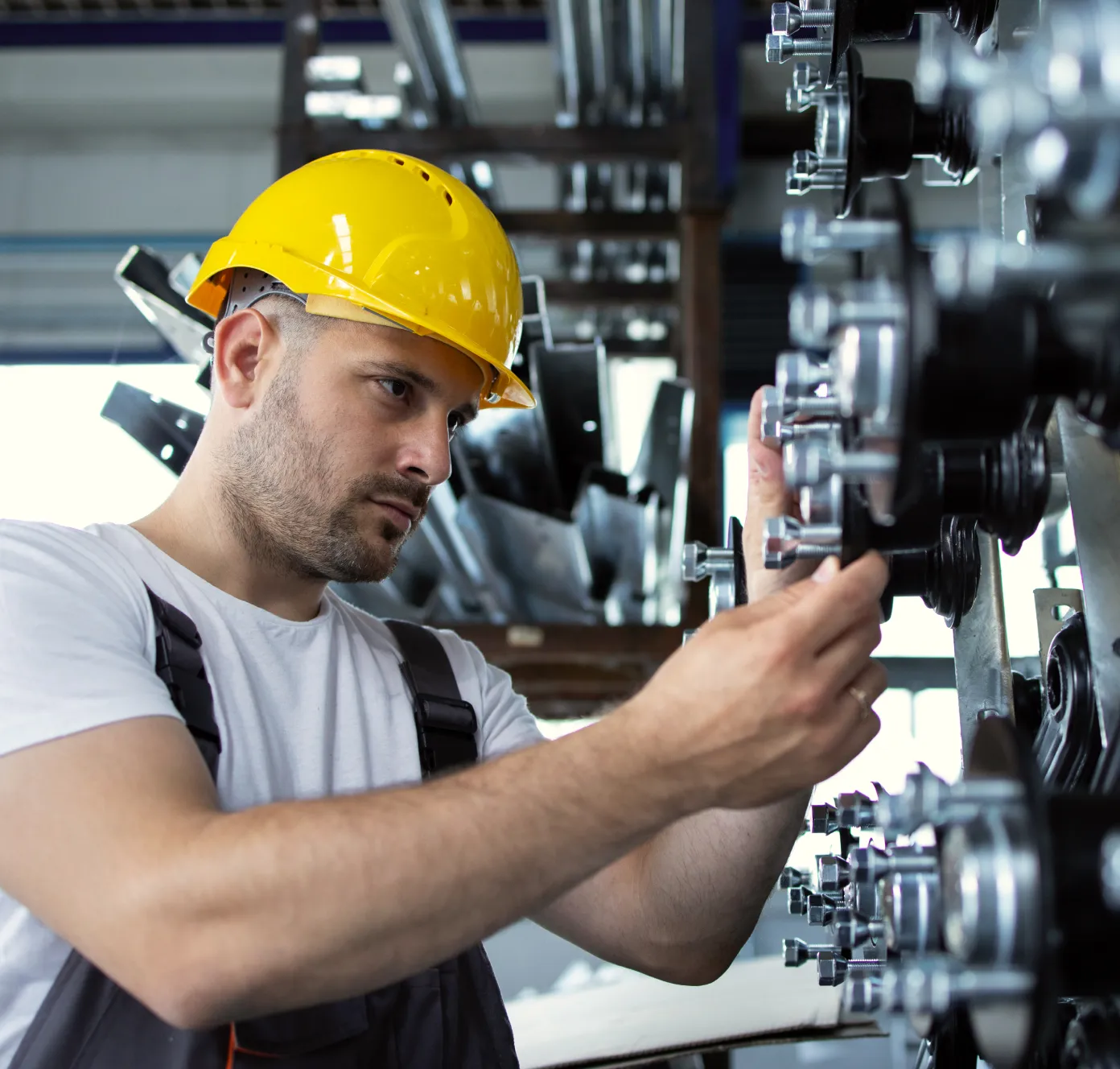
Main pain points & challenges
enspct advances manufacturing to the next level with smart technology created to match the realities and responsibilities of industrial work
- 01
Increasing demand for manufactured goods
The problemGlobal demand for manufactured goods is rising due to population growth, higher incomes, and urbanization. This places pressure on manufacturing companies to produce more, leading to increased demand for field service technicians to maintain and repair equipment.
Why field service would be needed?Field service software can help companies to meet increasing demand by automating tasks such as scheduling, dispatching, and reporting. This can free up technicians to focus on maintenance and repairs, which can help to improve equipment uptime and performance.
02Rising costs
The problemManufacturing companies are facing rising costs for raw materials, energy, and labor. This is making it more important for companies to operate efficiently and to minimize downtime.
Why field service would be needed?Field service software aids companies in cost reduction by automating tasks, streamlining workflows, and offering real-time operational insights. This enables early problem detection and resolution, preventing costly repairs and downtime.
03Labor shortages
The problemManaging extensive equipment at project sites hinders real-time asset monitoring, leading to increased downtime and costs due to insufficient preventive maintenance data.
Why field service would be needed?Software digitizes inspections, streamlines work orders, and provides equipment analytics, improving service delivery, asset uptime, and project timelines.
04Global competition
The problemManufacturing companies are facing increasing competition from global rivals. This is putting pressure on companies to reduce costs and improve efficiency.
Why field service would be needed?Field service software can help companies compete globally by providing them with the tools and resources they need to manage their assets and field service operations effectively.
05Complex supply chains
The problemManufacturing supply chains are getting more complex as companies source components and materials globally, making it challenging to monitor and maintain equipment.
Why field service would be needed?Field service software can help companies manage complex supply chains by providing a central repository for asset data and by automating maintenance and repair processes.
Field Service Innovation Powered by Enspct
Enspct streamlines quality control field operations for manufacturers with customizable templates to regularly check critical equipment, processes, and facility areas against safety and quality guidelines.
Enspct introduces paperless field operations so issues can be recorded and shared in real-time via user-friendly web and mobile applications.
Enspct's central platform provides valuable insights through analytics, improves transparency in fieldwork coordination, tracks corrective actions digitally, and enhances audit compliance with automated scheduling and reminders.
With enspct, manufacturers gain the visibility and control needed to address supply chain challenges stemming from inconsistencies, inefficiencies, and lack of visibility in field operations vital to quality and safety
Key Benefits in Manufacturing
Increased visibility
Track work orders, checklists, issues in real-time across all projects.
Streamlined workflows
Standardize processes for inspections, site walks, approvals, etc.
Enhanced organization
Manage documentation, submittals, RFIs digitally in one place.
Compliance management
Maintain compliance with automated reminders and alerts.
Performance optimization
Use data and metrics to identify areas of improvement.
Reduced rework
Identify defects early to prevent costly rework.
Faster turnarounds
Accelerate inspections, approvals, closeouts, and handover.
Mobility
Manage work from any device in the field or office.
Key features & benefits
Streamlined
field operations and visits
- Build customizable checklists for equipment, processes, and facilities
- Conduct digital field visits via web & mobile apps
- Record defects & observations in real-time with photos
- Complete field work faster with digital forms
Enhanced Quality Control
- Centralized data provides insights to continuously improve
- Automated scheduling ensures regular field operations
- Digital tracking of corrective actions increases accountability
- Compliance assurance for internal audits and external regulations
Increased Visibility
- All field jobs data in one place increases transparency
- Dashboards to identify recurring quality issues
- Analytics to optimize quality protocols over time
- Seamless sharing across production units and teams
Improved Compliance
- Schedule field jobs based on frequencies required by regulations
- Digitize forms for easier external agency submissions
- Maintain proper documentation for audits
- Automated reminders prevent missed field jobs
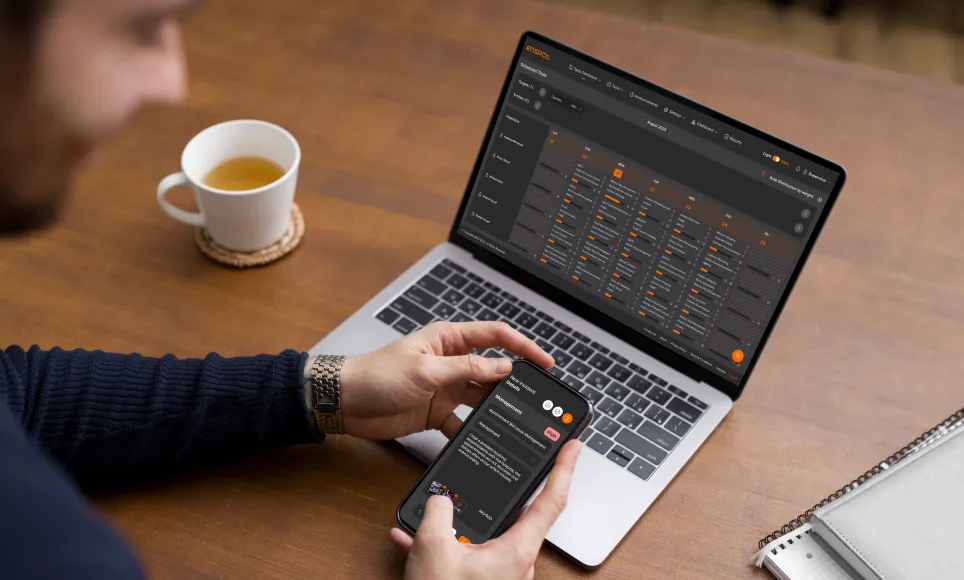
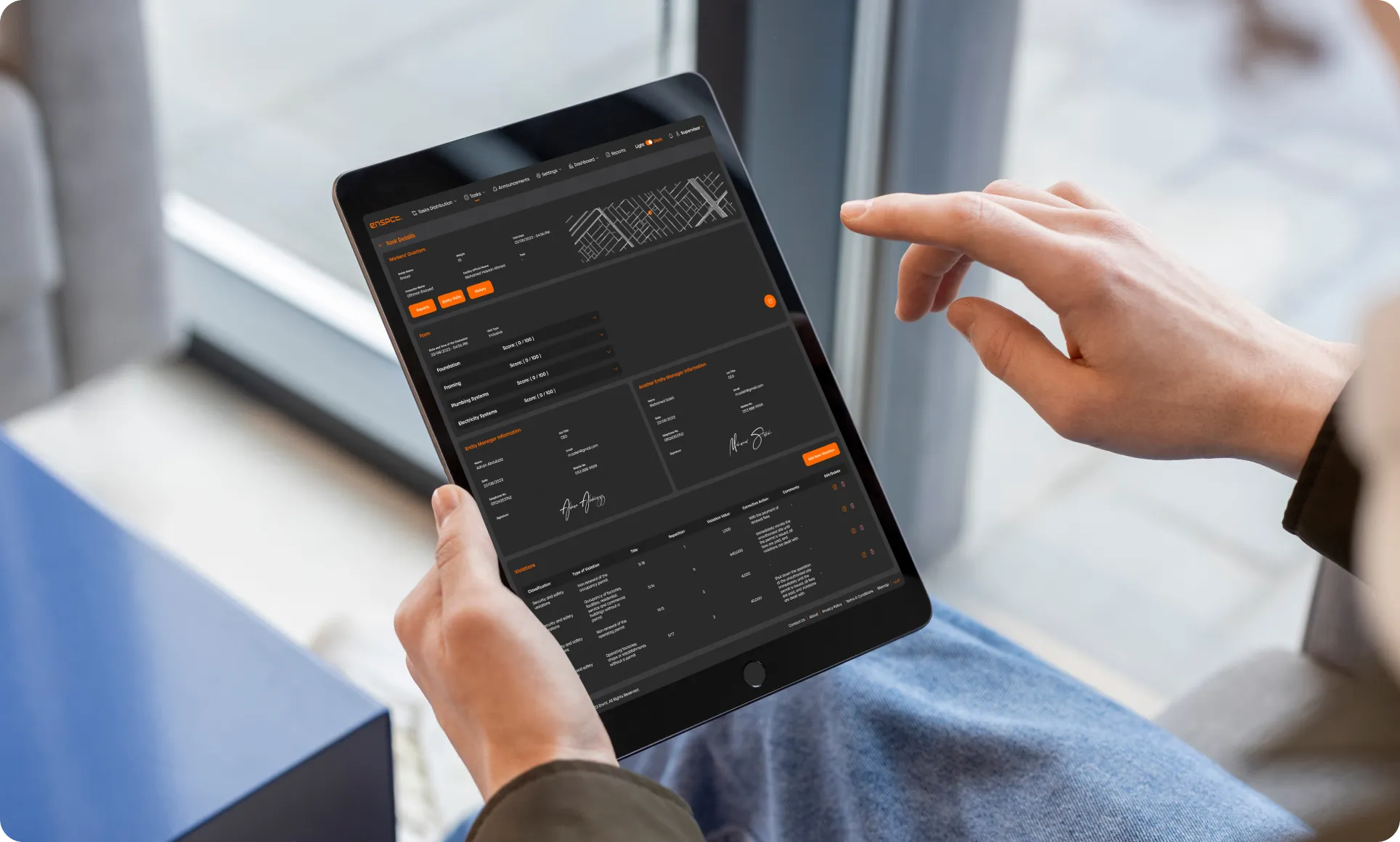
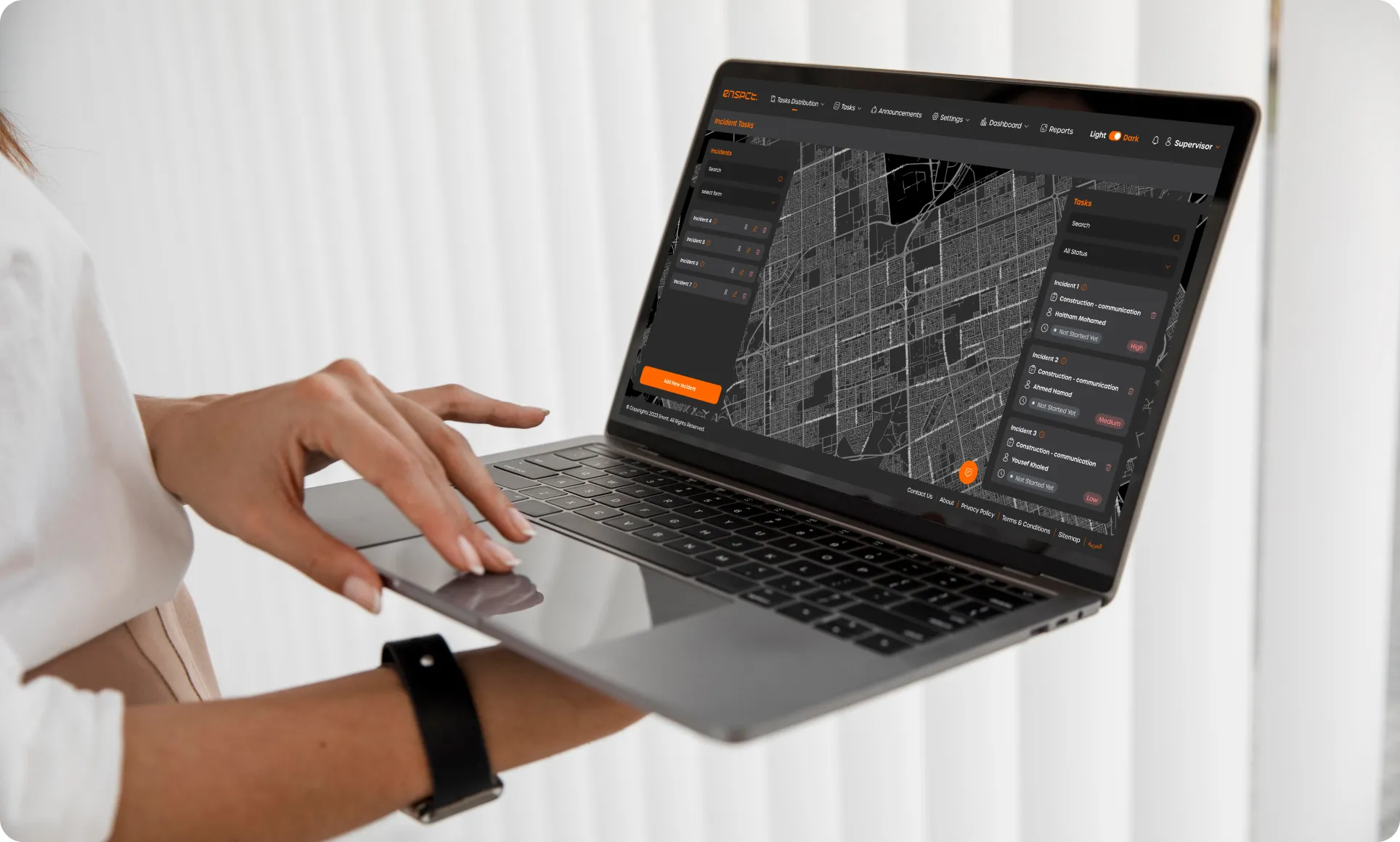
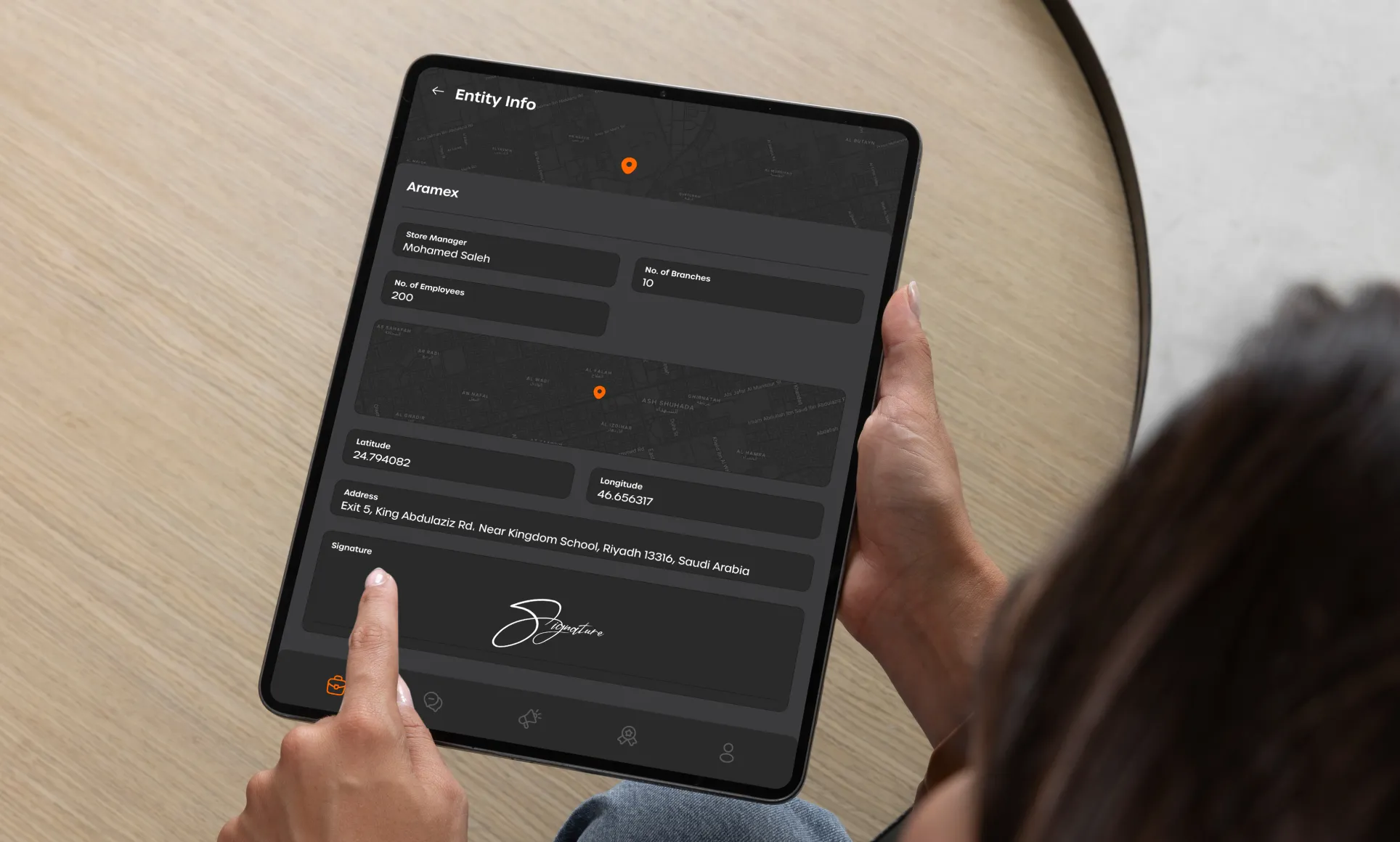